The Machines We Can(not) Do Without.
The automation of production is inevitable, but it requires people to bring ever higher value along the chain
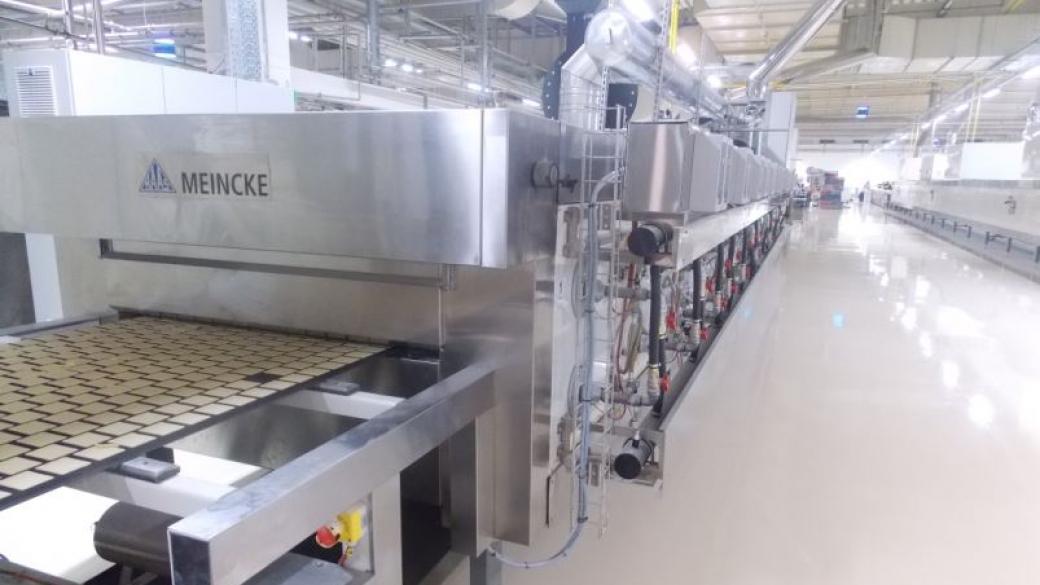
The emergency year of 2020 showed that business cannot do without people and without automation. The period of social isolation has caused a crisis in sectors where neither machines can do without human intervention, nor can people do without them, in order to move forward and remain sustainable.
According to a study by the Professional Association of Robotics and Automation (PARA) from 2019, Bulgarian robotics and automation in 2019 in numbers represents over 24 companies that develop robots, autonomous systems or software and components for such. Two smart factories are ready to work in Bulgaria. But has the emergency state made automation an inevitable necessity for production, or has it simply accelerated strategic intentions?
Kristian Mihailov, co-founder of PARA, says that for 25% of the surveyed companies in our country the main motivation for automation is quality improvement. The industries that most often benefit from the implementation of automated and robotic solutions are from the manufacturing sector, such as the food industry, the automotive industry, mechatronics.
The recession and the coronavirus are boosting automation. It is the market that is most often to blame for the introduction of innovations. A survey by consulting firm Earnst & Young in March found that 41% of the 3,000 largest companies are increasingly seeking to automate processes, which requires an additional budget. Until recently, the automation of production in our country was driven mostly by European funding.
Because of the crisis, there will be a delay in the search for automated solutions, due to purely market principles”, he predicts.
Nikolinka Hinkova, a member of the Board of directors of Mechatronics AD, has a different opinion. As the leader of a company that develops and manufactures unique automatic lines, she defines the pursuit of automation and digitalization as an internal awareness, reinforced by external circumstances. “Over 95% of our products are for export. Without innovation and without digitalization, we will not survive on the international market. For the most part, our production requires mental and precise work, a lot of knowledge and practical application of basic physical laws. The biggest challenge is the good theoretical training of engineers and their ability to apply it. But in the construction of new machines, digitalization allows for rapid preparation of programs for the manufacturing of parts; when collecting the details for the units, a digital warehouse is used, etc.”, she explains.
Magdalena Sergieva, HR director of the confectionery manufacturer Prestige 96, also shares the opinion that people are the engine of success - with their creative approach, vision, combinative thinking, analytical skills and risk management skills. Although some of the processes in the company are automated - both in the production itself and in receiving orders, planning and sales, in most cases the aim is to support people, not to replace them completely. “In the production process, this is the way to gradually automate all processes. Opportunities and investments for automation and digitalization are part of our business plan each year. The return from the project in a certain period, the impact it has on the quality of products and processes is considered. The state of the labour market and the forecasts for its development, the price and the quality of labour as an alternative to robotics also have a significant impact on the evaluation of projects.
The conversation is directed towards an idea that Kristian points out - the goal of any production is to shift the higher value from robots to humans. “An improperly planned replacement of a human with a robot can distort the process and lead to incorrect results. Very often the robots we see are used for specific programmable actions. Without proper process planning, there is no way to talk about subsequent economic efficiency”, he warns.
But before that, the manufacturing sector must find, train, attract and retain people to stand next to and work together with the machines. Mechatronics relies on young engineers, giving them the opportunity to work and study in the company. Nikolinka Hinkova also cites the experience of her colleagues from STS Pack Holding, according to whom digitalization and automation help people to be more productive, but require higher qualification. “In some industries, despite automation, labour is one of the main components in the formation of the cost. Incompetence, reluctance to work and poor management of the production process can dramatically increase the percentage of labour in the total cost of the product, and then it becomes unsaleable”, she explains.
“Use technology to help people, not people to help technology. The decision for automation and digitalization of the business should lead to improved efficiency and quality, and not be an end in itself under the influence of general trends and modern solutions on the market”, Magdalena Sergieva advises.
Kristian recommends simplifying production processes and training employees to bring higher value along the chain. Thus, they will be ready for the next stage of economic development – “all routine, monotonous activities to be eliminated and the potential of people to be directed to more skilled, creative operations”, Magdalena explains.
“For the final decision, the main factor is still not the mathematical models, but the experience and skills of the people who create solutions and manage processes based on these data and models. There are people behind every brand, product or service”, she concludes.