Marcel van der Hoek: In Bulgaria, the Digitization in the Industry Will Expand
ABB Group\'s Investments in the Country Continue to Grow
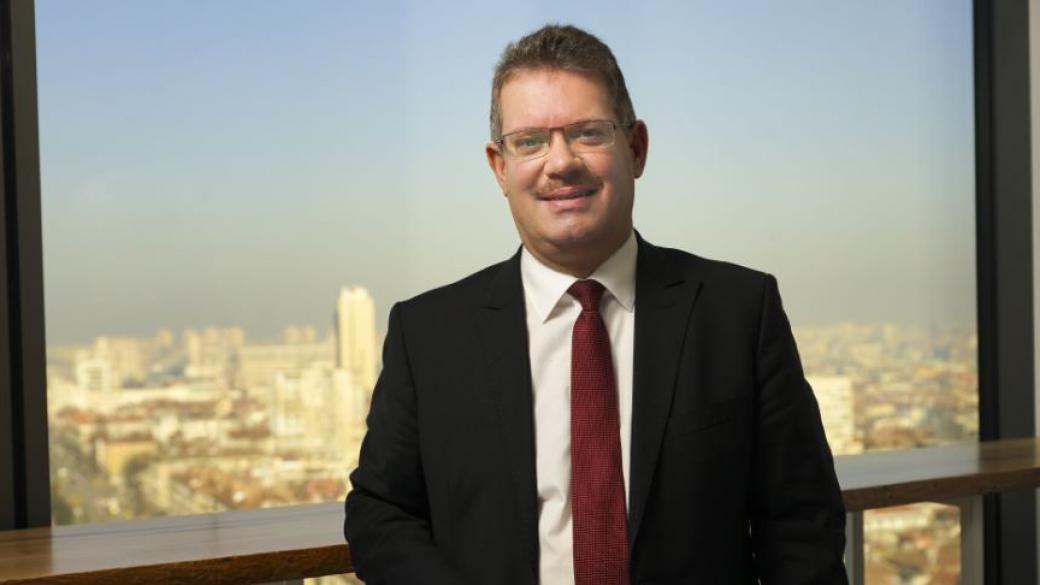
Marcel van der Hoek has been appointed as a Country Managing Directory of Bulgaria in the beginning of this year. He holds a Bachelor of Science degree in electrical engineering from Rotterdam University in the Netherlands. Between 1994 and 2005, Marcel van der Hoek has taken different positions in various countries for ABB in the area of general management, , sales, and business development. In 2005, he joined ABB Bulgaria, responsible for the Low Voltage products division, including the factory in Petrich and the sales organization. In 2007 he was appointed as local division manager for two divisions for the cluster Bulgaria, Romania, Moldova for Low Voltage Products and Discrete Automation and motion divisions. In 2011 Mr. van der Hoek joined ABB Slovakia as Country Manager and led the country for over six years until last year.
Mr.
van der Hoek, you joined the Bulgarian family of ABB in January this year. What
are your first impressions of the economic climate in the country and its
effects on the development of the local branch of the company?
I think that the general economic environment is good. The economy and consumption are increasing and likely to continue in next years. Also, the need for smarter technologies is on the rise, which helps companies also to become more productive and energy efficient. The ABB group investments in Bulgaria keep increasing. At the moment we employ over 2600 people in 5 locations (Four factories in Petrich, Rakovski and Sevelivo, one Turbocharging service station in Varna and main office in Sofia), and in most of the operations, we are still increasing our footprint. On demand side, we are growing by providing electrification, automation and robotization solutions. Even more, we’re also quite active in the innovative sectors like renewables and e-mobility.
International
companies frequently raise the issue that finding skilled labor is increasingly difficult in Bulgaria. Is
ABB facing similar challenges and how are you addressing those? Will the
increase automation have an impact on the job training and the requirements for
prospective workers?
Indeed, this is a big challenge for ABB and many other companies. In fact, ABB is offering great solutions to solve this problem, and we also apply some of them to our manufacturing units. Every production has bottlenecks or quality concerns in certain areas. By partially automating/robotizing these spots, you can increase your productivity by an amazing amount. Just to mention an example of how this could work: Let’s assume you have a production line with 100 people. Just adding 1-2 robots, may increase you output/productivity by 10-20 %. The people who worked in those areas can be diverted into another part of the production. You earn back your investment in very short time, In fact, if you didn’t invest your capacity is simply lower.
Just
a few months ago ABB introduced its single-arm collaborative robot. Without a
doubt, this is a great achievement in the history of robotics and
manufacturing. Is this robot already in
active use and how would this be affecting the human force?
Indeed, ABB already developed the first industrial robots in 1974 and continuously innovates since than. The latest development is in the area of collaborative robots. ABB has the YuMi (Dual arm) and now also a single arm version. The great thing about this is that you no longer need safety barriers and special areas. The robots can safely collaborate with humans, as all safety features are built-in. It also can be programmed by simply showing the arm how it should move. So if for example a worker is ill and you can’t get any replacement, you could put a collaborative robot in the line (Its lightweight). I spent my last seven years in ABB Slovakia, and there we sold already collaborative robots for many applications, mostly in the field of light items assembly. I am sure Bulgaria will follow already in next months.
We
are witnessing the blooming of the fourth industrial revolution with an
unprecedented invasion of technologies and smart solutions invading the
manufacturing processes. How is this affecting the management models? How does
“smart” look like in the context of management?
The consumers and end customers have many demands nowadays. For example, almost no two cars sold have same specifications. So there is a big trend not called mass production, but mass customization. To do this the old way is very expensive. Often change tools, materials, instruct people, using much floor space which makes the production costs expensive. If you automate or partially automate, you can have one line producing maybe 20-50 variances. Regarding management, it’s a complete change. By making production smarter, the management can concentrate more on implementing expansions, which will surely follow if you transformed the production to a cost-efficient setup in the first place.
How
is ABB- Bulgaria positioned when it comes to the implementation of smart
manufacturing decisions compared to the rest of the international branches of
the company?
Very well set up. What helps here a lot is that ABB already has a digital control center setup. We are already remotely monitoring many processes from our control center in Sofia. For example, we monitor the status of our installed-base fast chargers in Bulgaria, the power generation of Solar Parks we control, and processing data collected by the smart sensor. In other countries, this is not (yet) always the case, so I am very happy to see how progressive the approach is in Bulgaria.
Clean
Energy for all Europeans – is it a plausible or utopian future?
Clean energy is clearly on the rise. The challenges are to manage those energy flows, but ABB is on top of this topic with for example smart grids, and the technology is developing rapidly. Just as one Bulgarian example, recently, we helped a customer to improve the irrigation system of their orchard by replacing an old gasoline generator with a modern solar inverter, which allows us to monitor the performance remotely. The solution, which is both environmentally friendly and digital.
What
are your aspirations for the development of the company in Bulgaria in the
close future?
We aspire to work even closer with many customers and partners so that we can help them to become more efficient, competitive, and stable by providing solid and innovative solutions. Doing it successfully will result in more investments from our customers and future expansion in smarter and efficient products. Regarding our production base, I expect that the ABB group will continue to invest as well in nearly all locations in Bulgaria.